PLASTUB is your expert in plastic and elastomer extrusion
Thanks to its means of production, more than 40 years of know-how in extrusion and braiding (extrusion of plastics, silicone, TPE, FEP, PFA and other technical polymers) and an in-depth knowledge of its markets and applications, PLASTUB can offer a complete range of products that meet the specific requirements of its customers.
Our company designs and manufactures a complete range of extruded / braided products by offering you its expertise in the production of made-to-measure products developed for applications in extreme environments:
- severe mechanical stress
- aggressive chemical environments
- high temperatures
- and other uses subject to particular constraints
- When you choose PLASTUB, you can be sure that you are our top priority.
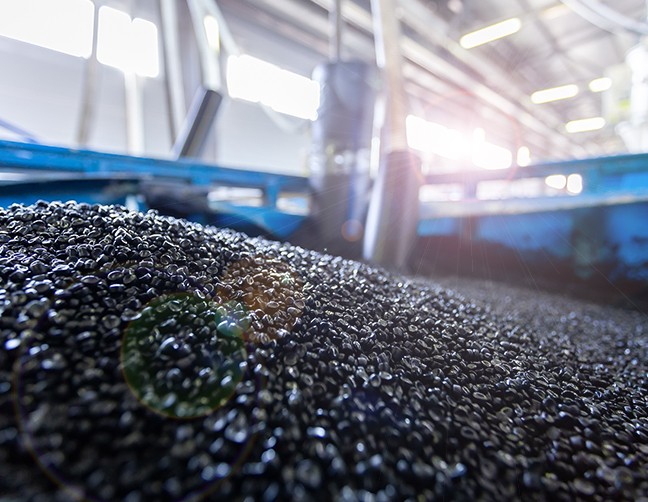
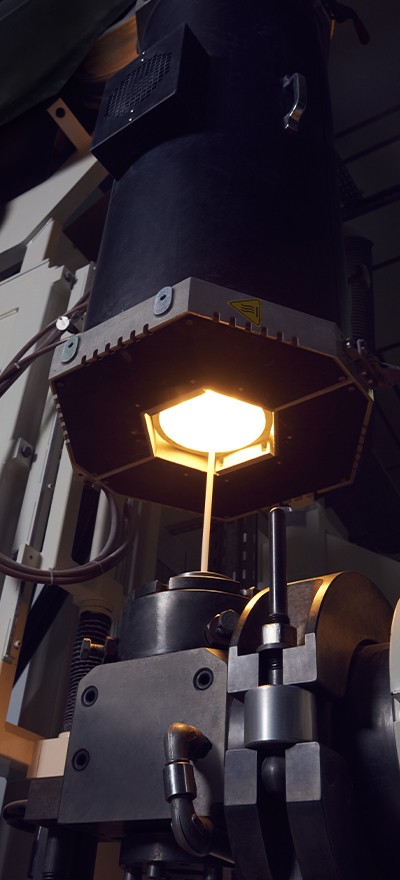
Extrusion and co-extrusion technologies
Extrusion is a continuous transformation technology used to produce finished or semi-finished products, such as sleevings, tubes, cords and profiles. It can be applied to almost all thermoplastic materials, as well as certain elastomers.
The principle of extrusion consists of transporting material from the feed zone to the tool. The material is compressed at a controlled temperature throughout the process, so that it is shaped in the tool, then hardens at the take-off.
Single-screw extruders are by far the most widely used machines in the plastic transformation industry. They are made up of a feed zone for the material, a melt zone comprising an Archimedes screw in a thermally regulated barrel and an extrusion head containing a tool. It is the tool that is used to determine the shape and cross-section of the extruded product.
The distinction must be made between:
- The extrusion of thermoplastics (PVC, TPE, PE, PA, PP, PU, etc.): pellets, known as compounds, are heated in the mixing and compression phase in the extruder. The molten and pressurised material is then shaped in the tool. The extruded product is immediately cooled in tanks of chilled water, before being packaged. Most thermoplastic products can be crushed, re-pelletised and extruded again, meaning that they are recyclable.
- Extrusion of silicone elastomer: a catalysed rubber is kept a low temperature in the mixing and compression phases, then shaped raw in the extruder. The extruded product is immediately vulcanised in an oven before being packaged. The vulcanisation process is irreversible, so it is difficult to recycle silicones.
Co-extrusion is similar to conventional extrusion and is used to make long finished products, such as cables or multi-tubes.
The principle consists of coating a support with a material using an extruder that is perpendicular to the line. Therefore, the production line consists of a continuous uncoiling system that feeds the extruder head. Thermoplastic products are then cooled, while silicone elastomer products are vulcanised, before packaging.